Hot Product
Refractory Knowledge
The Manufacturing Process of Magnesia Bricks
Date:2016-03-11 11:21 From:Zhengzhou Sunrise Refractory Author:admin
The manufacturing process of magnesia bricks is the basis for the production of magnesia refractories and even basic refractories. The manufacturing process of high purity magnesia brick and direct bonded magnesia chrome brick are the similar to it. What are different are just parameters such as the raw materials, purity, molding pressure and firing temperature.
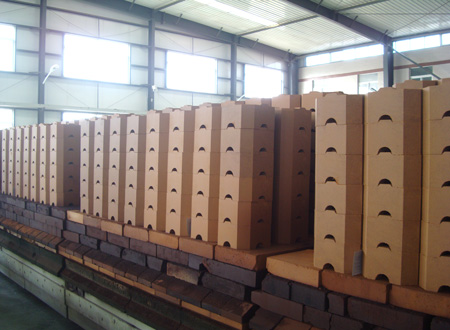
1) Raw materials
The main raw material of the magnesia brick is just the common sintered magnesia sand. The magnesia sand is made by sintering the magnesite and calcined coke in a vertical kiln. So, the content of SiO2 and CaO, especially SiO2, is much higher than that of that in the magnesite. The main requirements on it are the chemical composition and sintering degree. The MgO content should be more than 87%, CaO less than 0.5% and SiO2 less than 5.0%. meanwhile, it should be sintered well. The density should not be less than 3.18 g/cm3 and ignition loss less than 0.3%. There should be no nodular objects and black blocks should be as less as possible.
2) The particle composition and ingredients
Particles should be in line with the principle of closest packing and in favor of the sintering. The critical particle size should be determined according to the degree of sintering and the exterior dimensions and unit weight of magnesia brick. 4 mm, 3 mm, 2.5 mm and 2 mm can be chosen. For bricks with a big unit weight, critical particle size can be increased appropriately. Size distribution is generally: the critical size to 0.5 mm 55%-60%, 0.5 ~ 0.088 mm 5%-10% and less than 0.088 mm 35%-40%.
In production, crushed scrap bricks are added, but its amount is generally not more than 15%. Or in the molding process, crushed scrap bricks are directly incorporated into the mud for molding.
The binding agent added is sulfite waste liquors (density 1.2-1.25 g/cm3) or MgCl2 solution (brine).
3) Kneading
In the wheel rolling machine or sand mixer, the granular materials, pulp waste and powder are successively added. The total mixing time should be not less than 10 min. in order to limit the CaO content and improve the sintering degree, the aging of the mixture is canceled.
4) Molding
Sintered magnesia sand is a barren material and has low moisture content. Generally there is no over-pressed scrap due to the compressing of the air. Therefore, high-pressure molding is used to increase its density to 2.95 g/cm3 or more. This will help to improve the performance of refractory bricks.
5) Drying
Physical and chemical changes in the drying process include evaporation of water and hydration process of magnesia sand. The initial stage requires higher temperature, but high temperature can speed up the hydration of magnesia sand and cause cracking. Especially in the late stage, since the influence of the thermal conductivity is greater than that of the wet conduction, high temperature is not conducive to the exclusion of moisture.
In the tunnel dryer, the inlet temperature of the drying medium is generally controlled at 100-120℃. The outlet temperature of waste gas is generally controlled at 40-60℃. In order to ensure certain strength, bricks should contain about 0.6% moisture after dried.
During the drying process, the main reason for scrap bricks is net cracks. This is because a large amount of hydrate is generated in bricks after molded. If it is controlled well, there should be no scrap. After dried, bricks should be loaded into the firing kiln in time to avoid moisture absorption and powdering.
6) Firing
The firing of magnesia bricks can be carried out conducted in a down draft kiln or a tunnel kiln. Their softening temperature under load is low and their strength is reduced when the binding agent is invalid. Therefore, the brick stack should not be too high, generally about 0.8 m.
Inquiry:
If you have any questions or good suggestions on our products and site, or if you want to know more information about our products, please write them and send to us, a representative will contact you within one business day. We guarantee that your information will not be divulged to the third party.